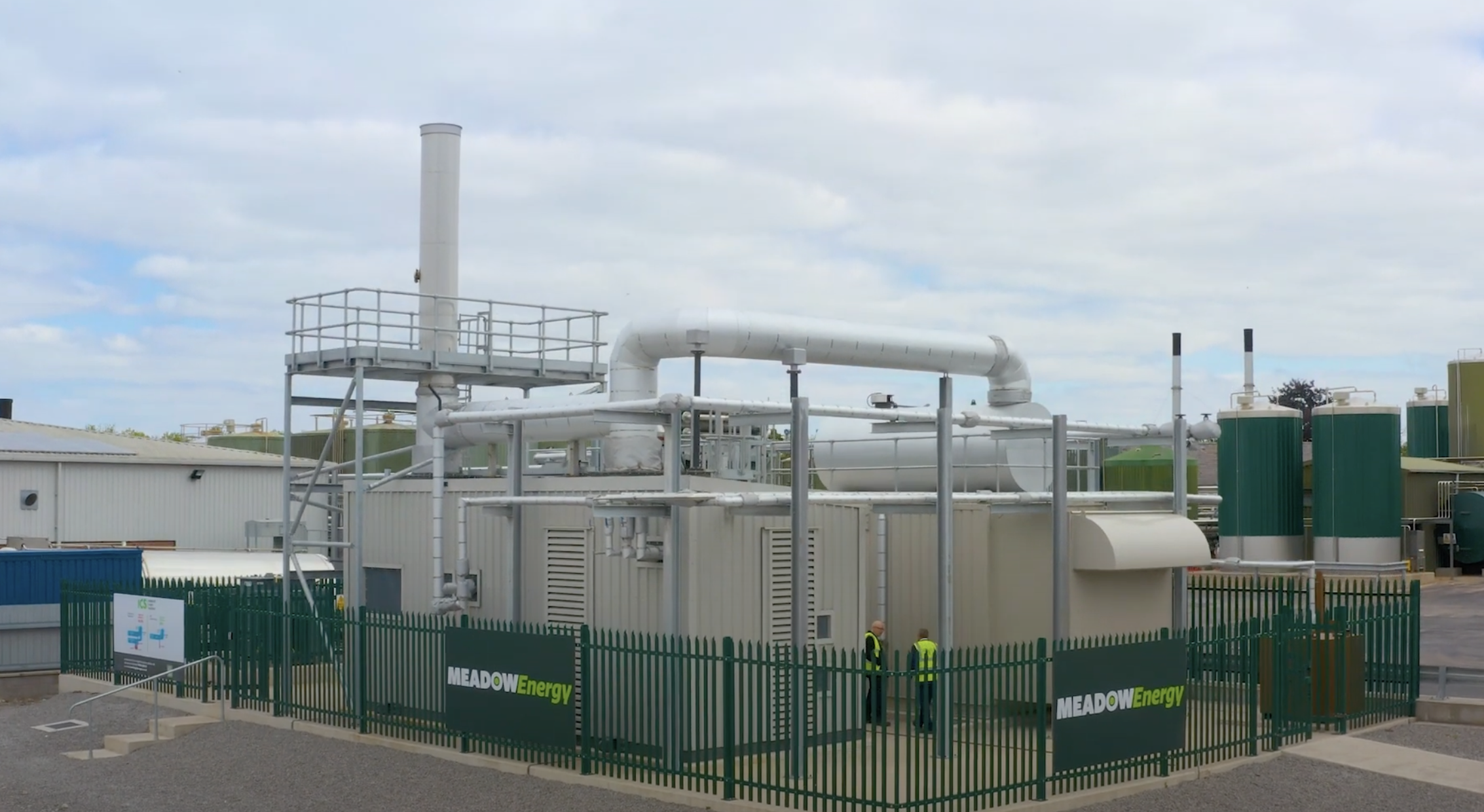
23 May ICS Meadow Foods
Meadow Foods has completed the installation of a new Combined Heat and Power (CHP) facility at its Chester site, delivered in partnership with ICS – specialists in the design, installation, and maintenance of CHP systems for manufacturing environments.
The newly commissioned system generates 1.6 megawatts of electricity and produces over a tonne of steam, offering substantial energy and cost-saving benefits to the site’s operations.
ICS founder Paul Doherty explains that CHP systems are well-established and widely used across the industrial sector in the UK and internationally. “The benefits can range from £500,000 up to £2 million per annum depending on the size of the facility,” he says. “It’s proven, reliable technology that suits energy-intensive environments like food production.”
Meadow Foods initially asked ICS to carry out a feasibility study to explore whether CHP could be a viable option for its Chester dairy. The study showed that installing a CHP unit would be of clear benefit to the site’s production processes.
The project was overseen by ICS Project Manager Michael Farnell. The team handled all civil construction work before installing the 1.6 megawatt CHP system and a containerised waste heat boiler. The boiler captures excess heat from the CHP process to produce steam, which is then fed into the factory’s existing steam system – reducing the load on traditional gas boilers.
The electricity generated is stepped up via a transformer and fed directly into the site’s high-voltage ring main. With the system using around 2.5 units of gas to generate one unit of electricity, it provides a far more cost-effective solution than drawing electricity from the grid.
In addition to the cheaper on-site electricity, the production of over a tonne of steam means the site’s existing gas boilers don’t need to work as hard, further reducing overall gas consumption.
Both the CHP unit and the waste heat boiler arrive containerised, making installation straightforward and allowing them to integrate quickly into existing infrastructure.
The end result is an annual cost saving estimated between £700,000 and £750,000.
Together, Meadow Foods and ICS have developed Meadow Energy – a bespoke, site-specific solution that delivers meaningful efficiency gains.