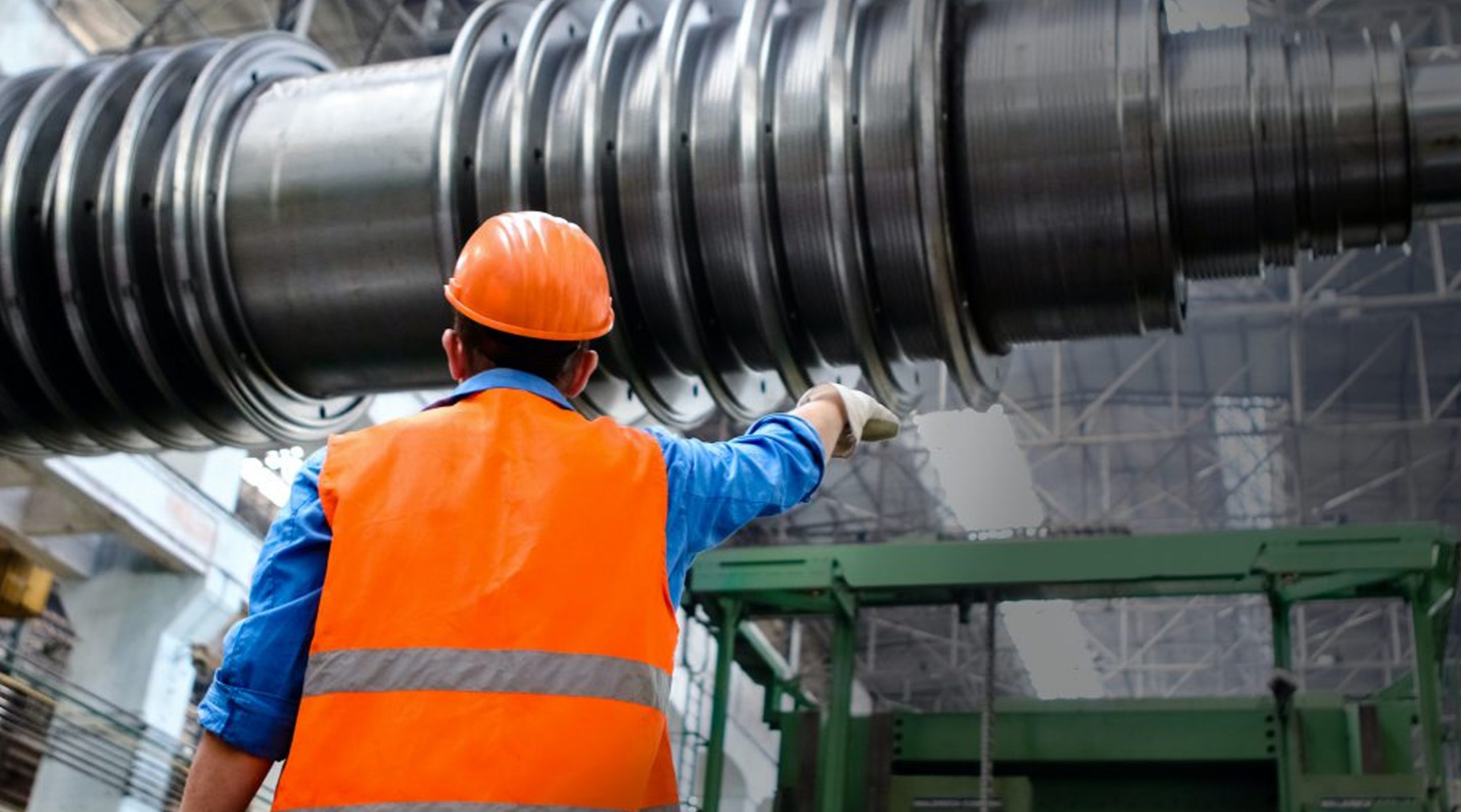
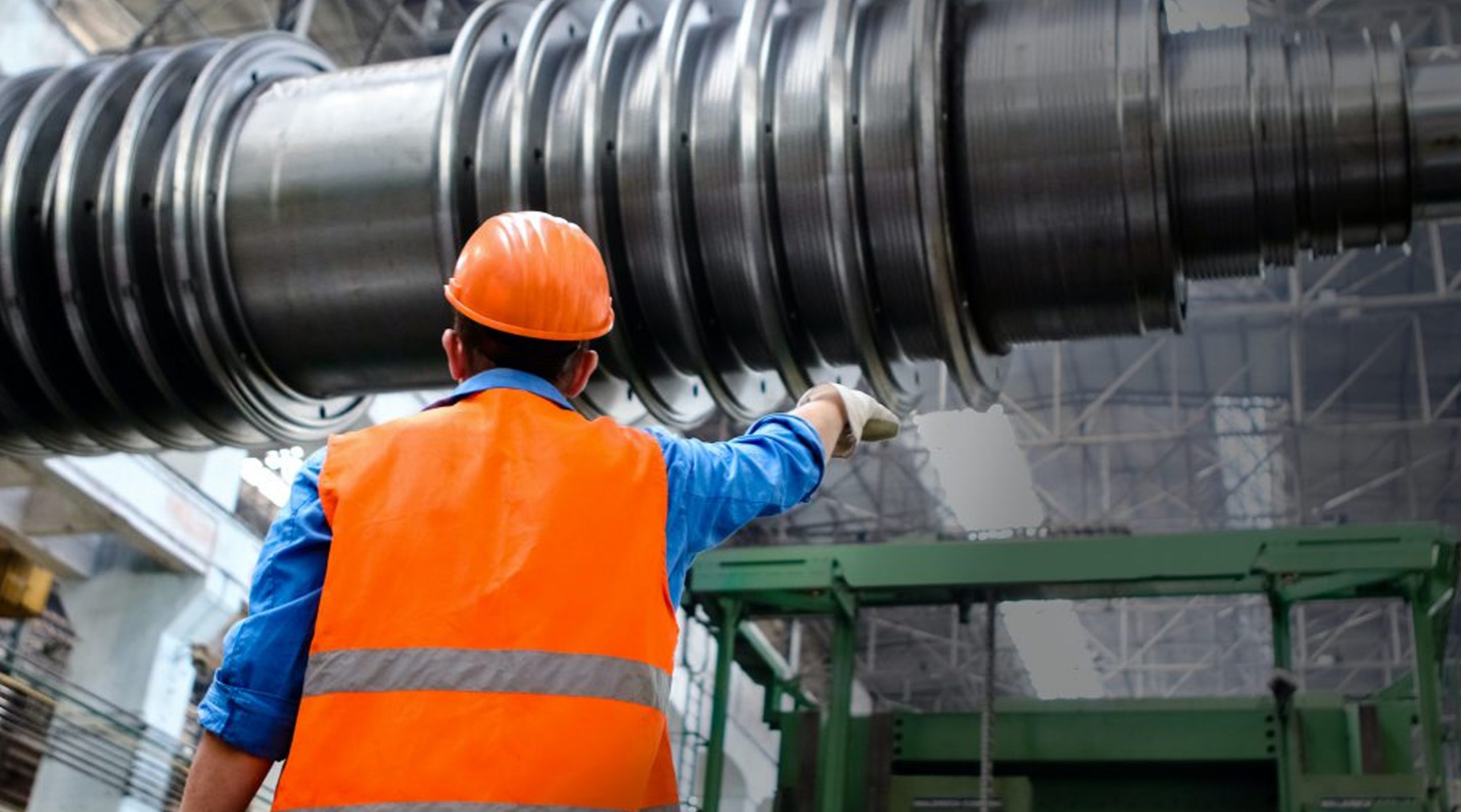
Until comparatively recently cogeneration in industry was focussed on large scale industrial sites with many Mega Watts (MW) of demand for both electricity and heat. These days though with soaring prices for electricity, cogeneration is viable for sites with a sub 1MW electrical demand and the cost savings are considerable. Using natural gas engines as a prime mover with outputs typically in the range 1MW to 2.5MW a cogeneration system can be developed for almost any site which will significantly reduce energy costs.
Power generation alone will yield energy cost savings on most sites, but by applying a range of heat recovery measures to the engines, savings are maximised. Heat recovery from gas engines was traditionally focussed on low temperature hot water (LTHW) with heat recovered from both the engine jacket and exhaust. Now, for many industrial applications, engine exhaust heat is converted to steam with the jacket water remaining as LTHW. Steam generation is viable with systems delivering 1MW or less of electricity as noted above using either a waste heat boiler or a combination boiler which in essence is a standard boiler with an exhaust gas heat recovery section.
Using LTHW from the engine, heat recovery can also be configured to generate chilled water via an absorption chiller with a typical supply temperature of around 6°C. Where chilled water only is required a dual energy absorption chiller using the engine jacket water and exhaust gases only can be used which offers a higher efficiency (COP) than a standard absorption chiller. If sub-zero chilling is required, an ammonia-based absorption chiller will meet this requirement and can be applied to both liquids and gases.
Contact us today to see how we can assist you to engineer a cogeneration system tailored to your needs and significantly reduce your energy costs.